Steel Fabrication Melbourne: Craftsmanship Satisfies Technology
Wiki Article
Leading Methods for Optimizing Steel Fabrication Processes for Optimum Efficiency
From meticulous format preparing to embracing sophisticated innovations, the quest for maximum efficiency in steel manufacture involves a complex method. Allow's discover exactly how these strategies can reinvent steel fabrication procedures, paving the means for unmatched efficiency and competitiveness in the sector.Effective Format Planning
In the realm of steel construction procedures, efficient and critical design preparation plays a critical duty in streamlining manufacturing workflows and maximizing functional performance. The layout of a steel construction center straight influences the effectiveness of operations, product flow, and employee productivity. By meticulously creating the setup of machinery, workstations, storage areas, and material handling tools, companies can substantially minimize unneeded activity, decrease product dealing with times, and optimize the general manufacturing procedure.A reliable design strategy considers aspects such as operations sequences, distance of workstations, material handling paths, and safety laws. It intends to develop a structured and logical circulation of tasks from basic material consumption to the final item send off. Via reliable format preparation, firms can get rid of bottlenecks, minimize manufacturing downtime, and boost the general operational effectiveness of the steel fabrication process.
Additionally, a well-balanced design plan enables better utilization of readily available room, enhanced communication in between employees, and enhanced safety techniques within the facility. In general, investing time and sources in establishing an efficient format strategy can produce substantial advantages in terms of enhanced productivity and cost savings for steel manufacture companies.
Advanced Cutting Technologies
Using cutting-edge technologies in steel manufacture processes boosts accuracy, effectiveness, and general manufacturing high quality. In addition, plasma reducing modern technology has actually additionally changed steel fabrication by enabling swift and precise cutting through electrically conductive products. By including these innovative reducing modern technologies right into steel manufacture procedures, makers can dramatically raise performance, lower manufacturing times, and eventually improve the high quality of their products.Automated Welding Systems

Among the key benefits of automated welding systems is their ability to preserve a high level of precision throughout the welding procedure. The precision offered by these systems makes sure that welds are uniform and satisfy the called for specs, bring about stronger and extra trustworthy metal structures. In addition, automated welding systems decrease the danger of human mistake, leading to less defects and remodel.
Furthermore, these systems can deal with intricate welding tasks easily, consisting of welding in tight spaces or on rounded surface areas. This flexibility makes automated welding systems ideal for a large range of steel manufacture applications, from large industrial jobs to detailed personalized designs. Generally, the execution of automated welding systems in steel fabrication procedures dramatically enhances effectiveness, quality, and total job results.
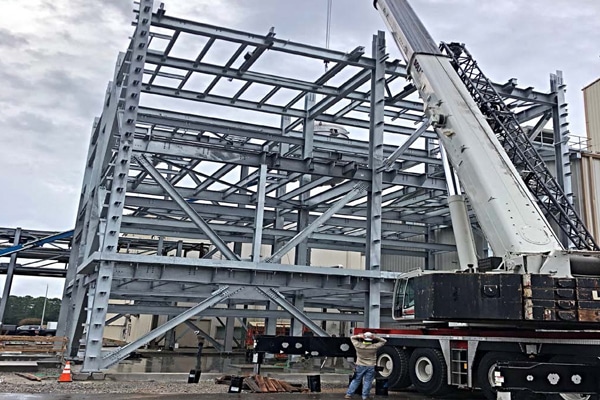
Inventory Management Solutions
Enhancing operational efficiency and improving processes, efficient stock administration services play a vital duty in maximizing internet steel manufacture procedures. By carrying out durable stock administration systems, steel construction companies can make sure that the best products are offered when needed, reducing disruptions and hold-ups in manufacturing routines. Utilizing sophisticated software solutions enables real-time tracking of supply levels, enabling accurate projecting of product demands and avoiding stockouts or overstock situations.In addition, supply monitoring options help in minimizing bring costs associated with excess supply and enhance capital by lining up inventory degrees with actual demand. By classifying materials based upon use frequency and criticality, makers can prioritize purchase and storage area allocation, better improving functional efficiency. Additionally, carrying out barcode or RFID technology promotes accurate supply tracking and streamlines the monitoring of product movements within the center.
Continuous Process Renovation
To develop upon the gains made through reliable stock monitoring services, the emphasis now moves in the direction of driving constant procedure renovation within steel manufacture operations. Constant procedure improvement is an organized method focused on enhancing performance, reducing waste, and boosting overall quality throughout the manufacture process. By carrying out a society of constant enhancement, steel construction business can recognize traffic jams, simplify workflows, and enhance sources to maximize productivity.One trick element of continual process improvement in steel fabrication is the routine evaluation and evaluation of manufacturing procedures. This entails gathering feedback from workers, checking vital efficiency indicators, and identifying areas for enhancement. By leveraging data-driven insights, firms can make educated decisions to drive significant modifications that positively affect operations.
Moreover, adopting lean manufacturing principles can considerably contribute to process improvement in steel fabrication. Alpha reo. Techniques such as worth stream mapping, five organization, and Kaizen events can help eliminate non-value-added activities, systematize procedures, and promote a culture of development and continuous learning within content the company
Verdict
Finally, enhancing steel manufacture processes for maximum effectiveness calls for careful planning, making use of advanced cutting innovations, implementing automated welding systems, managing stock properly, and continuously improving processes. By integrating these methods, suppliers can improve productivity, decrease expenses, and boost total efficiency in the steel manufacture industry.Through reliable layout planning, companies can get rid of bottlenecks, decrease production downtime, and improve the general operational effectiveness of the steel construction procedure. Alpha reo.
Utilizing advanced technologies in steel fabrication processes boosts accuracy, performance, and total manufacturing quality. By incorporating these advanced cutting technologies into steel fabrication procedures, suppliers can significantly raise performance, my link minimize production times, and eventually enhance the quality of their products.
Generally, the implementation of automated welding systems in steel construction procedures considerably boosts performance, quality, and general project outcomes.
One trick aspect of continuous procedure renovation in steel construction is the normal evaluation and analysis of manufacturing procedures. (metal fabrication melbourne)
Report this wiki page